ABOUT CEMEX Nicaragua
The CEMEX company was founded in 1906 in Mexico and thanks to its visionary management during the 20th century it consolidated itself as one of the leading companies in the production of cements and concretes in the world. It is a global leader in the building materials industry, with more than 100 years of experience and a presence in more than 50 countries. CEMEX Nicaragua is a market leader and has been part of this great global family
since 2001.
Overview
The CEMEX plant in San Rafael del Sur is the only one in Nicaragua that performs the complete cement production process and additionally offers a 24/7 dispatch service.
CEMEX, the third largest cement producer in the world, saw the great potential for this industry in Nicaragua and began negotiations with the government in 2000. Since then, the company has made millions in investments in state-of-the-art technology in all its processes, has increased productivity by operating in harmony with nature and offers market leading sustainable products. Likewise, it invests in industrial safety, occupational hygiene, customer service and especially in the well-being of its employees and the communities where they operate
The Challenge
The plant in San Rafael del Sur receives traffic from different heavy vehicles, from those that transport raw material for production, to units of product delivered and withdrawn where bagged and bulk cement is dispatched.
The cement dispatch process had different stages to serve customers. Each of these stages have different waiting and attention times to complete the cycle.
The supervision of the clients' route was carried out manually, supported by radio communicators and mobile phones. This route started from an external parking lot to the scale exit, on a route that stretches for more than 600 meters.
The Solution
In its continuous improvement cycle, CEMEX listened to its customers and prioritized a plan to optimize the dispatch route, reorganizing and implementing technology to reduce bottlenecks that affected cycle time.
Once operational improvements had been established to reduce time, we proceeded to look for an automation option to monitor the customers' route and to guarantee the coordination and visibility of the service in real time.
CEMEX conducted a search for systems, adding a Public RFP in which ACF demonstrated that it had the experience and track record to carry out a project of this magnitude. The first step was a visit to the San Rafael del Sur plant, led by one of our consulting experts. There, the information was collected in each of the stages, to observe the opportunities for improvement.
A modelling document was created that allowed framing the stages, times, and sub-processes within each of the phases. To carry out the project, it was necessary to implement the Q-Flow modules, which intervene in each of the stages of the process:
Self-management kiosk: The self-management kiosk issues a shift ticket that guarantees the driver his space and is evidence that he will be dispatched, being able to choose to wait in his truck and not in the waiting room.
Digital signage: A screen was displayed throughout the plant with information on the different stages of the process: shift number, truck license plate number, order number, number of units per station and service times. Screens allow CEMEX carriers and personnel to have visibility at all times.
Notifications via SMS (Connect): Once the carrier arrives at the plant to pick up product and enters their data in the self-management kiosk or point of entry, a notification via SMS of their order number, truck license plate number and time is sent
to the customer's cell phone arrival. Likewise, you receive another message at the end of your upload notifying the service time.
Custom console: Due to the safety characteristics and exposure to elements such as sun, dust and rain, a portable console was parameterized in screens that allow handling with safety gloves and in which the dispatchers find all the information to manage the queue of clients, having clear information and visibility of each service.
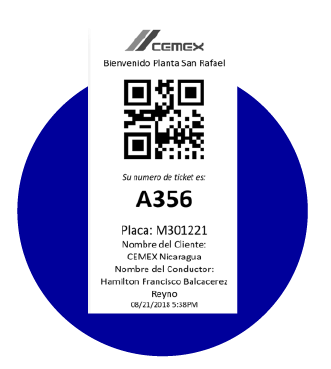
Signalling via QR codes: The self-management kiosk gives the carrier a ticket number that contains a QR code. This allows a checkpoint by means of an infrared reader on the scale. This automatically activates the display on dispatch screens, indicating that that shift is already entering the plant.
Reports: Analysis panels were installed through the reports module of the administrative console to facilitate monitoring and continuous improvement.
Email notifications are sent to the plant manager when a case has longer than desired wait times.
The reports also included the results of the satisfaction survey for carriers, which is carried out for each entrance to the plant and is available in the self-management kiosk process.
The Results
- Decrease of more than 50% in service cycle times, which provides a significant improvement in the customer experience, which is reflected in the Net Promoter Score (NPS) - satisfaction measurement that CEMEX performs quarterly.
- Optimization of resources according to demand through reports that allow obtaining information on days and peak hours.
- Process automation through QR Codes in the scale area.
- Reduction of customer stress levels, through SMS notifications and Info page screens that provide information on shift positioning.
- Decrease in complaints and claims about agility in offices, where this issue no longer represents a dissatisfaction alert
- Culture of agile and safe attention by always having visibility and transparency of the time cycle
Want to know more?
We are more than happy to investigate how we can work with you to transform your customers’ experiences every time they interact with your organization and dramatically increase your operational performance. Speak with our experts value the opportunity to combine their knowledge and experience with technology that enables an improved journey design and optimal customer experience.